Rotary kiln is just another name for rotary kiln equipment. Rotary kiln equipment consists of: cylinder, belt, supporting wheel, blocking wheel, transmission device, sealing device, brick block ring, block ring, chain, metal heat exchange. Device, manhole door, fire hood and connection accessories.
Rotary kiln can calcinate many different materials and is a common roasting equipment. And now, in order to control the quality of the finished clinker, an automatic control device is used, so that a large amount of raw material can be processed with low energy consumption, and the quality of equipment calcination can be improved. The characteristics of high output and low energy are achieved, so that the equipment can enhance energy conservation while burning high-quality clinker. Adding an automatic control device can reduce the manpower of the rotary kiln equipment, then what are the uses of the rotary kiln equipment, what is the composition structure and working principle?
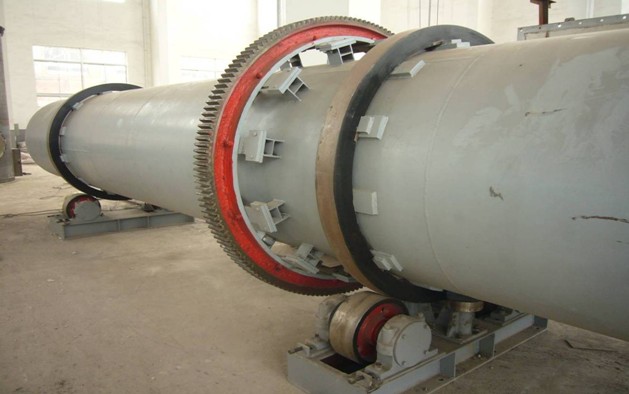
SOIL REMEDIATION ROTARY KILN
Use of rotary kiln:
1. In the building materials industry, in addition to calcining cement clinker, rotary kiln is also used for calcining clay, limestone, and slag drying; etc. In the production of refractory materials, rotary kiln is used as the raw material to stabilize the size and increase the strength. , And then processed.
2. During the beneficiation process, a rotary kiln is used to magnetize and roast the lean iron ore, so that the original weak magnetism of the ore is changed to strong magnetism to facilitate magnetic separation.
3. In the chemical industry, rotary kiln is used to produce soda, calcined phosphate fertilizer, barium sulfide, etc. In the 1960s, a new process for producing phosphoric acid using a rotary kiln was invented. This method has the advantages of low energy consumption, low electricity consumption, no need for sulfuric acid, and the use of low and medium grade phosphate rock.
4. The entire production process of cement is summarized as “two mills and one burn”, of which “one burn” is the process of firing the raw meal prepared by grinding and turning it into clinker under the high temperature of a rotary kiln. Therefore, the rotary kiln is the main machine in cement production, commonly known as the “heart” of cement plants.
5. In terms of environmental protection, developed countries in the world have used cement kilns to incinerate hazardous waste and garbage for more than 20 years. This not only reduces waste and harmless it, but also uses waste as fuel to save pulverized coal. Recycling of waste.
Working principle of rotary kiln:
(1) There are chemical and physical reactions inside the rotary kiln, and the calcination phase is divided into three phases, the preheating phase, the calcination phase, and the cooling phase. When the limestone is calcined, the heat between the material and the calcination zone is exchanged back and forth in the area of the rotary kiln, so that the moisture of the raw material is evaporated, and under the condition of uneven heating, the volume expands and the ultimate compressive strength decreases. When the internal temperature reached 700 degrees Celsius, it entered the calcination zone.
(2) The calcination zone is in the middle of the rotary kiln.
When the material enters the area, the fuel starts to burn under the condition of the blower’s combustion. Can release a lot of heat, so the temperature in the kiln will rise slowly, when the temperature reaches a certain range. At this point, temperature control is required. For example, the decomposition rate of limestone and the gas generated in this case will be relatively large, which is conducive to the calcination of raw meal into clinker. The generated gas is discharged by the air flow, at this time the clinker begins to enter the cooling zone.
(3) The cooling zone is in the lower half of the kiln body of the rotary kiln equipment. At this time, the residual clinker will not be decomposed in this area. At this time, the material after being calcined can be cooled. The relative position of each area is also relatively stable. Can not be separated indiscriminately, it is necessary to operate according to changes in raw material and fuel conditions. The materials can be better utilized after cooling inside the kiln body.